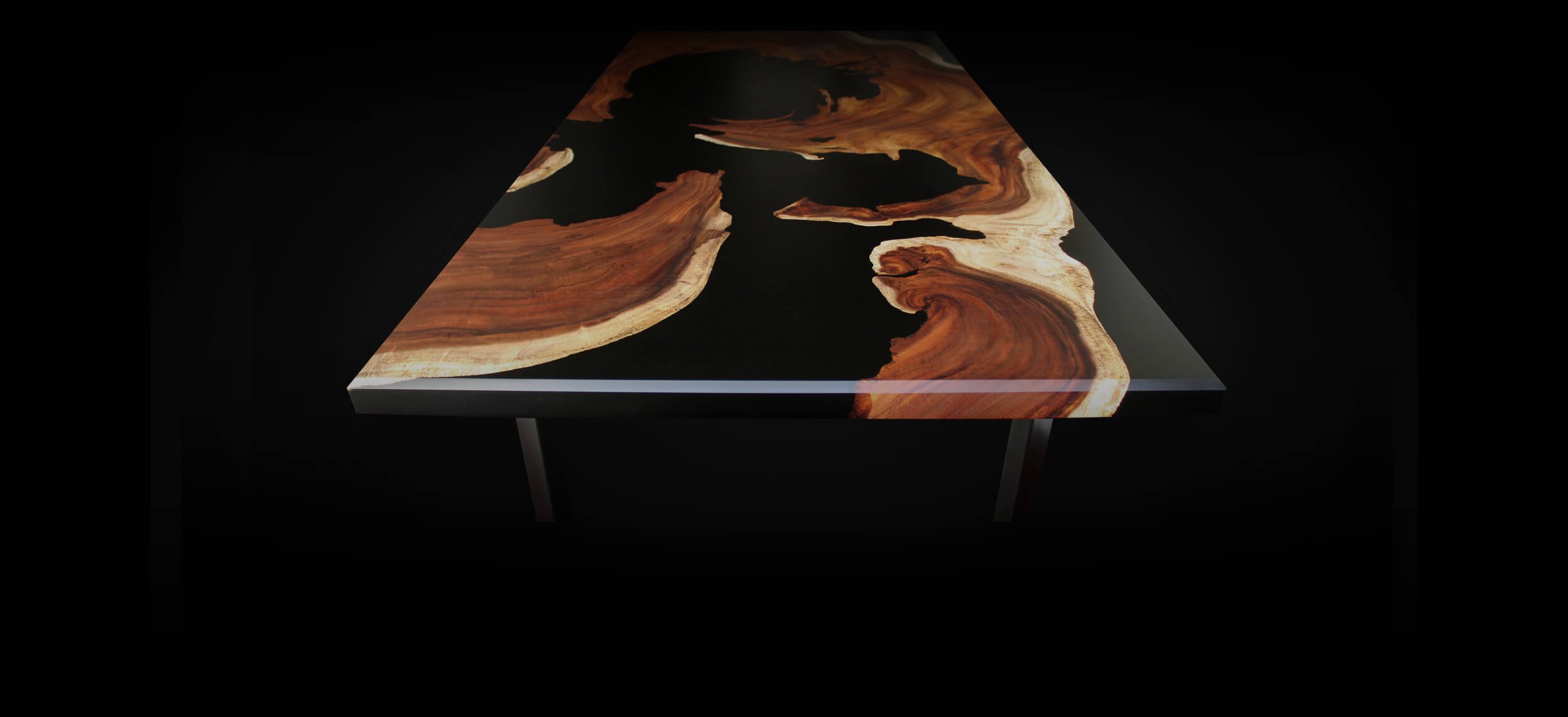
Custom Wood Tables
Handmade in North Carolina
I transform salvaged wood into functional art. My specialty is custom built epoxy resin river tables, live edge slab tables, and unique solid wood furniture for commercial and home use.
-
Cookie Slab Tables
-
Live Edge Tables
-
Epoxy River Tables
How does it work?
It all begins with an idea. I am passionate about woodworking, and while the steps to creating heirloom quality furniture can be daunting, I will personally help guide you along the way. Serving the Raleigh and Apex NC area, I provide personal face to face consultations.
-
Decide the final style of your desired table; a more abstract cookie slab, live edge single board, or epoxy river running down the middle.
-
The best looking, most durable wood species for epoxy tables are hardwoods such as Yew, Elm, Oak, Hickory, Monkey Pod, or Black Walnut.
-
Kiln drying kills insects and removes wood moisture in months versus air drying which takes years. This helps prevent cupping and warping.
-
For visualization, I build a template that will allow you to see the inside of your finished table. I will also help you choose the final legs/base.
Building & pouring
-
Slabs usually have rot, bark, and soft spots that need to be removed. This step is critical to ensure no soft spots show up in the final finish application.
-
Sealing wood edges prevents any staining that can happen from dyed resin penetrating the wood. It also helps minimize air bubbles during epoxy curing.
-
Making an aquarium tight mold helps prevent epoxy leaks. This step is very critical, no cutting corners. I use only premium materials to build world class molds.
-
Many variables in this critical step including air temperature, calculating quantity, dye or pigment, proper mixing/pouring, and torching air bubbles.
Flattening & finishing
-
The mold is removed after 2 weeks ensuring maximum epoxy hardness. The mold release allows the table to be safely removed, along with all screws and caulk.
-
The table is run through a commercial 50” planer to get it as flat as possible. All imperfections are filled with CA glue, then sanding to an ultra-smooth finish begins.
-
From here I add 2 coats of Rubio Monocoat, a plant-based, hardwax oil wood finish that is 0% VOC, durable, matte and keeps the natural look & feel of the wood.
-
Professional threaded inserts with CA glue are used making it extremely durable and possible to assemble & disassemble anytime. No more screwing and bolting directly into the wood.
